Forging
With a grand total of two closed-die, multi-directional forging presses, ELLWOOD Crankshaft Group boasts the world's largest and most efficient among them! These exceptional machines give ECG an unparalleled edge in the market, thanks to their ability to streamline the manufacturing process. By utilizing multi-directional forging practices, ECG is able to create crankshaft forgings with a continuous grain flow structure, which is absolutely essential for the highest quality products. Additionally, each die is expertly designed to produce near-net shape forgings, which not only saves on material cost but also machining time.
.jpg)
Continuous Grain Flow
ECG's unique forging process utilizes specialized presses that allow for the production of forgings with continuous grain flow. This innovative method provides a host of advantages over other forging methods. By following the contours of the throw with the centerline of the starting bar through the middle of the pin, grain flow remains continuous and identical in every crank throw. Compared to hammer or open-die forged parts, this process yields improved material and reduces waste. Additionally, forgings produced with continuous grain flow exhibit superior fatigue and impact properties in critical regions, making them ideal for high-stress applications. With ECG's advanced forging technology, you can trust that your components will be crafted to the highest quality standards.
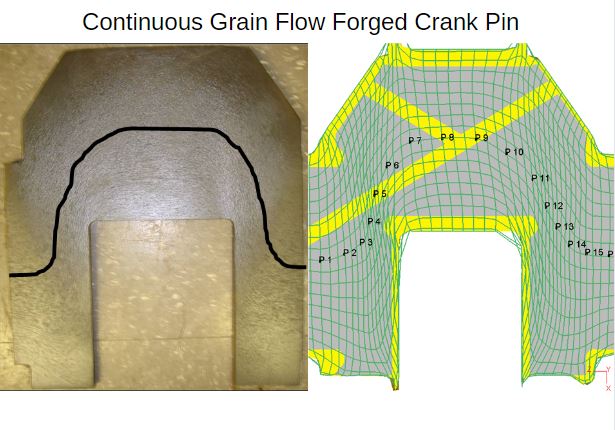
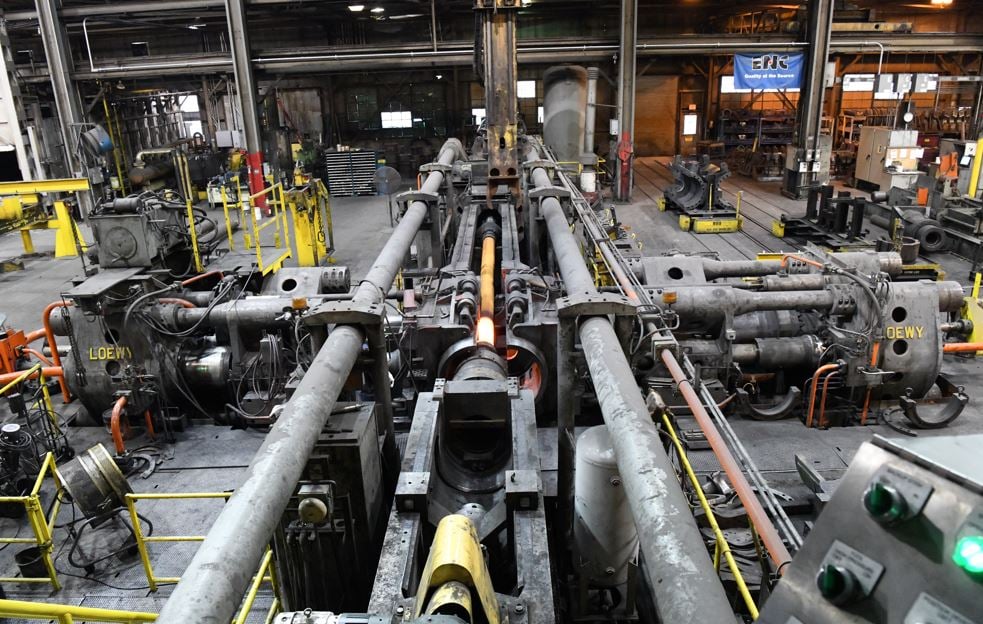

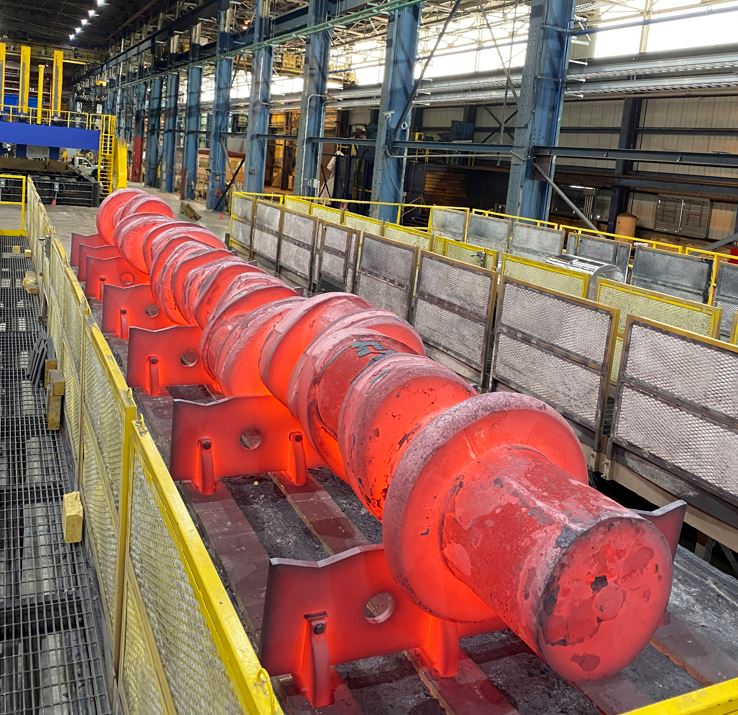
Open Die Forging
Much of the raw material utilized by ELLWOOD Crankshaft Group is high-quality open die forged bar and billet. This material is able to be procured through ELLWOOD City Forge Group, the open-die division of ELLWOOD. ECFG operates 3 forging presses up to 5,000 tons at 2 locations in Pennsylvania. All bar and billet is produced using sound center forging practices to ensure the starting stock quality needed to produce critical power components.
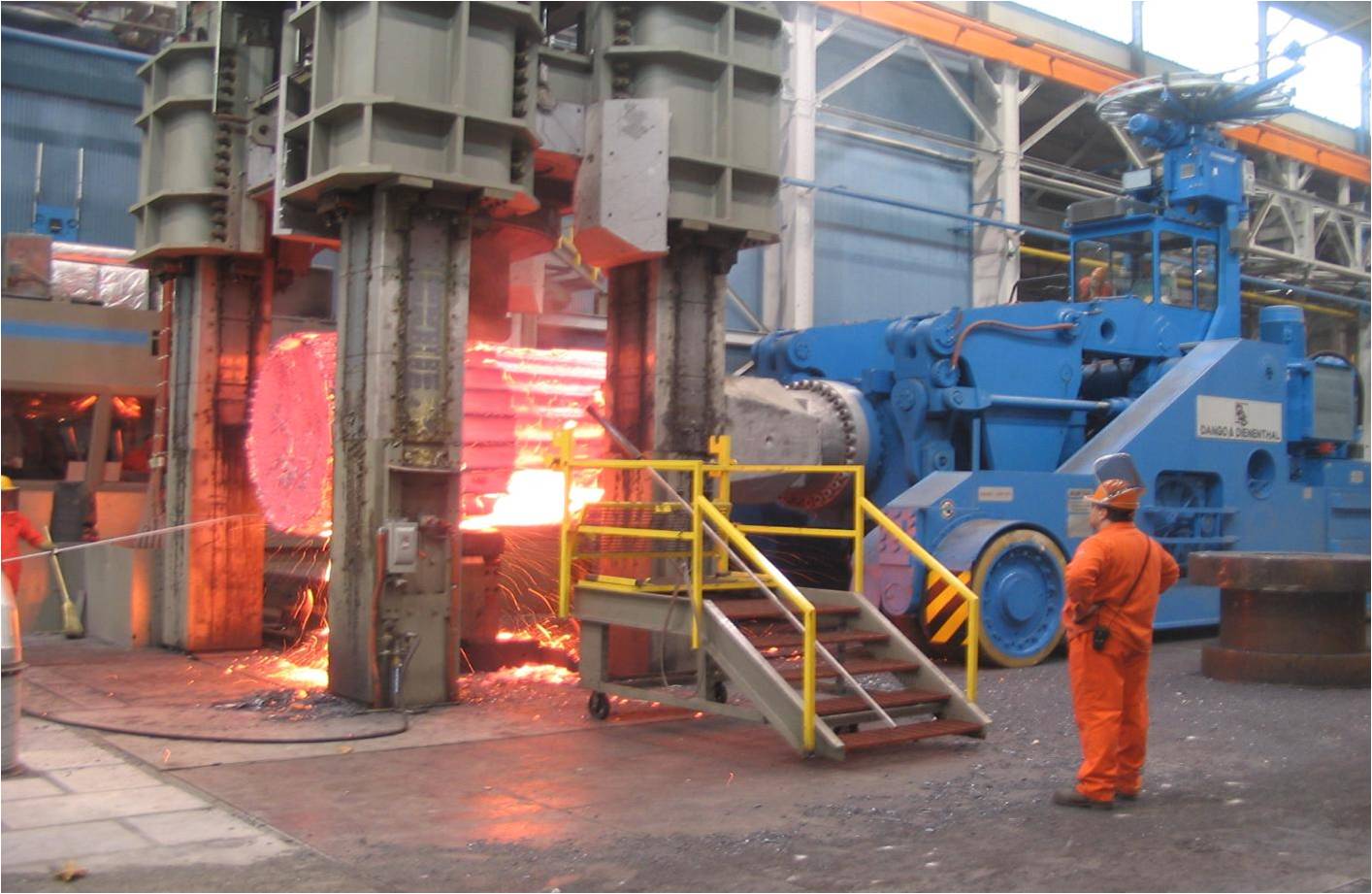